What are the methods for current limiting tests of electric vehicle controllers
Introduction: As a core component of the power system, the current-limiting function of the electric vehicle controller directly affects the safety, energy efficiency, and lifespan of the entire vehicle. The current-limiting design aims to prevent damage to the motor, battery, or controller due to overcurrent. Therefore, strict current-limiting tests are a crucial step in the research and development and production processes. This article will systematically introduce the common methods of current-limiting tests for electric vehicle controllers and their application scenarios.
2025-03-26
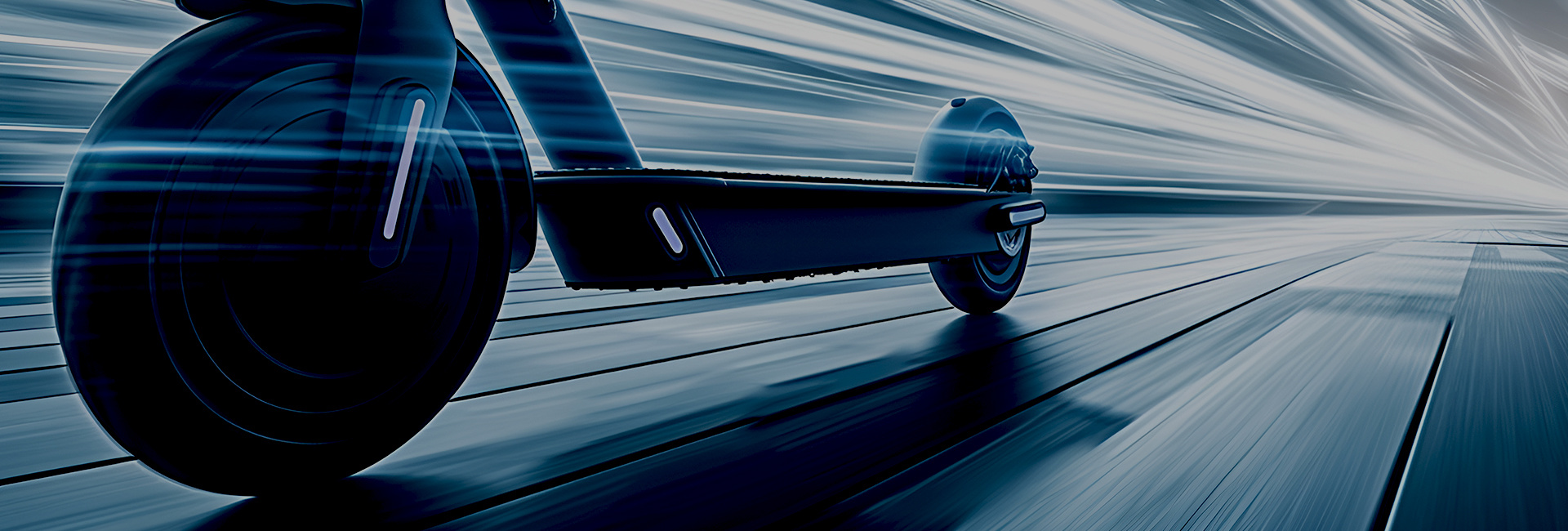
Introduction: As a core component of the power system, the current-limiting function of the electric vehicle controller directly affects the safety, energy efficiency, and lifespan of the entire vehicle. The current-limiting design aims to prevent damage to the motor, battery, or controller due to overcurrent. Therefore, strict current-limiting tests are a crucial step in the research and development and production processes. This article will systematically introduce the common methods of current-limiting tests for electric vehicle controllers and their application scenarios.
I. Static Current Testing Method
Principle
The operating state of the motor is simulated by an external adjustable power supply or electronic load. The current is gradually increased to the threshold of the controller to detect the trigger point of the current limiting function.
Implementation Steps
Connect the adjustable DC power supply to the input terminal of the controller.
2. Use a high-precision ammeter (with an error of no more than 0.5%) in series to monitor the current.
3. Gradually increase the output current of the power supply and record the current value when the current-limiting protection is activated.
Repeat the test 3 to 5 times to verify stability.
Advantages: The test environment is controllable and the data has high repeatability.
Limitation: It cannot reflect the true performance under dynamic working conditions.
II. Dynamic Load Testing Method
Principle
During the actual operation of the motor, the dynamic response characteristics of the controller are verified by triggering the current limiting mechanism through sudden load changes.
Test plan:
Use a dynamometer to simulate heavy load conditions such as steep slopes and acceleration.
Suddenly increase the mechanical resistance when the motor is at its peak power state.
Capture the current waveform through an oscilloscope and analyze:
Throttling response time (typical value should be < 50 ms)
Current overshoot (should be less than 10% of the rated value)
Restore stability
Key indicators:
Phase synchronization between Hall sensor signal and PWM output
The temperature rise rate of the MOSFET switch (requires the use of an infrared thermal imager)
III. Temperature Correlation Test
Test Design:
Build a temperature-controlled test chamber and conduct current-limiting tests at different ambient temperatures ranging from -20℃ to 65℃, with particular attention to:
Current margin during low-temperature cold start
2. Thermal derating characteristics under high-temperature conditions
3. The interlocking logic between the temperature sensor (NTC) and the current limiting threshold
Data collection:
Thermocouples should be placed at key positions on the controller PCB, such as the MOSFET heat sink and current sampling resistor.
Record the temperature-limiting threshold change curve (which should conform to the designed thermal derating curve)
IV. Fault Injection Testing
Test category:
Hardware failure simulation:
Short-circuit the current sampling resistor
Disconnect the Hall sensor wiring harness.
Simulate a sudden change in power supply voltage (12V to 16V instantaneous impulse)
2. Software Agreement Testing:
Tampering with the CAN bus current calibration parameters
Inject abnormal PWM duty cycle command
Acceptance criteria:
Trigger the hardware protection circuit within 200 ms.
The accuracy rate of fault code storage is ≥ 99.9%.
V. Road Test on Actual Roads
Test Procedure:
Select a comprehensive test section that includes long slopes and continuous curves.
2. Conduct under full load conditions:
A 30-minute uphill test
Rapid acceleration - braking cycle test (0 - full speed / 10-second cycle)
3. Monitoring with an on-board data recorder:
Output current ripple of battery pack
Harmonic distortion rate of motor phase current
Temperature gradient variation of the controller heat sink
Conclusion
By comprehensively applying multi-dimensional methods such as static testing, dynamic testing, environmental testing, and actual road testing, the current limiting performance of the controller can be comprehensively evaluated. With the popularization of SiC power devices and intelligent algorithms, it is recommended to add:
Verification of Current Sampling Accuracy at High-Frequency Switching (>50kHz)
Testing of Adaptive Rate Limiting Algorithm Based on Machine Learning
By establishing a complete testing system, the reliability of the controller under complex working conditions can be effectively enhanced, promoting the development of core electric vehicle technologies towards a higher safety level.
Previous